High Capacity Vertical Roller Grinding Mill Equipment
Application of vertical roller grinding mill equipment:
Vertical roller grinding mill equipment are suitable for huge capacity producing, widely used in grinding non-flammable and non-explosive materials under 9.3(the Moh's hardness), such as quartz, feldspar, calcite, talcum, barite, fluorite, iron ore, copper ore quartz, especially for slag, cement clinker, zircon sand, fly ash and carborundum, coal, etc.
Advantages of vertical roller grinding mill equipment:
1. Grinding mill equipment in the market designed as a cement grinder and not a modified raw mill
2. Simple layout and fewer machines in the mill circuit ensure high run-factor and low maintenance costs
3. Roller and table profile improve operating stability and reliability
4. Special design features for iron removal during grinding minimize wear
5. Optimal wear protection on all internal surfaces extends lifetime
6. Flexibility to operate with reduced number of rollers guarantees long-term availability
7. Segmented roller wear parts made of the hardest possible material without the risk of cracking; very suitable for hard facing
8. High grinding efficiency: save 20~30% power consumption compared with the ball mill. With the increasing of moisture content, it can save more and more electricity.
Working Principle of Vertical Roller Grinding Mill Equipment:
The grinding disc is driving by motor through reducer. The material falls to grinding disc from the feed opening. The materials are driven to the edge of disc by the centrifugal force and crushed into fine powders by rollers. Then, the hot air from the nozzle take the fine powder to high efficiency classifier. The qualified powder is taken by the air to the powder collector to be collected, while the unqualified powder is sent back for regrinding.
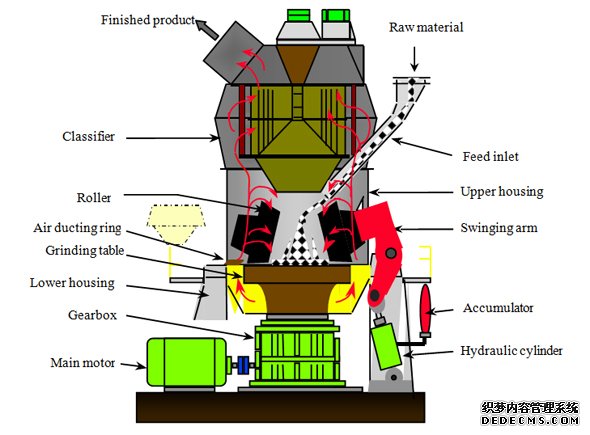
Technical data of vertical roller grinding mill equipment:
If you want to know more about vertical roller grinding mill equipment, please leave us a message or chat with our on line service now.
Vertical roller grinding mill equipment are suitable for huge capacity producing, widely used in grinding non-flammable and non-explosive materials under 9.3(the Moh's hardness), such as quartz, feldspar, calcite, talcum, barite, fluorite, iron ore, copper ore quartz, especially for slag, cement clinker, zircon sand, fly ash and carborundum, coal, etc.
Advantages of vertical roller grinding mill equipment:
1. Grinding mill equipment in the market designed as a cement grinder and not a modified raw mill
2. Simple layout and fewer machines in the mill circuit ensure high run-factor and low maintenance costs
3. Roller and table profile improve operating stability and reliability
4. Special design features for iron removal during grinding minimize wear
5. Optimal wear protection on all internal surfaces extends lifetime
6. Flexibility to operate with reduced number of rollers guarantees long-term availability
7. Segmented roller wear parts made of the hardest possible material without the risk of cracking; very suitable for hard facing
8. High grinding efficiency: save 20~30% power consumption compared with the ball mill. With the increasing of moisture content, it can save more and more electricity.
Working Principle of Vertical Roller Grinding Mill Equipment:
The grinding disc is driving by motor through reducer. The material falls to grinding disc from the feed opening. The materials are driven to the edge of disc by the centrifugal force and crushed into fine powders by rollers. Then, the hot air from the nozzle take the fine powder to high efficiency classifier. The qualified powder is taken by the air to the powder collector to be collected, while the unqualified powder is sent back for regrinding.
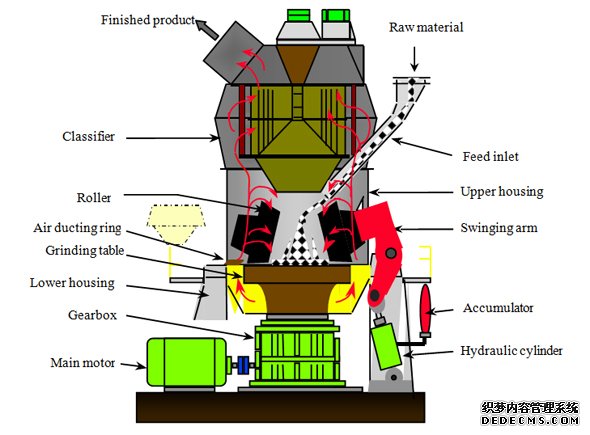
Technical data of vertical roller grinding mill equipment:
Model | HRM53 | HRM38 | HRM36 | HRM34 | HRM32 | HRM28 | HRM27 | HRM25 | HRM22 | HRM17 |
Grinding disc diameter (mm) | 5300 | 3800 | 3600 | 3400 | 3200 | 2800 | 2700 | 2500 | 2200 | 1700 |
Amount of grinding rods | 4 | 4 | 4 | 4 | 4 | 3 | 3 | 2 | 2 | 2 |
Installation power(kW) | 3600~4000 | 2000~2500 | 1800~2240 | 1600~1800 | 1400~1600 | 800~1250 | 800~1000 | 710~900 | 400~500 | 200~250 |
Power of powder separator(kW) | 200 | 132 | 110 | 90 | 90 | 75 | 55 | 45 | 30 | 15 |
Max feeding size (mm) | ≤100 | ≤85 | ≤80 | ≤70 | ≤70 | ≤70 | ≤65 | ≤70 | ≤50 | ≤40 |
Feeding moisture (%) | 6 | 6 | 6 | 6 | 6 | 6 | 6 | 6 | 6 | 6 |
Moisture of final products (%) | 0.5 | 0.5 | 0.5 | 0.5 | 0.5 | 0.5 | 0.5 | 0.5 | 0.5 | 0.5 |
Grindability index of raw materials (Wi) | 7.5~13 | 7.5~13 | 7.5~13 | 7.5~13 | 7.5~13 | 7.5~13 | 7.5~13 | 7.5~13 | 7.5~13 | 7.5~13 |
Productivity (t/h) | 330~510 | 185~280 | 170~260 | 140~210 | 125~190 | 85~130 | 78~120 | 60~90 | 40~65 | 22~33 |
Model | HRM1300M | HRM1400M | HRM1500M | HRM1700M | HRM1900M |
Grinding disc diameter mm | Φ1300 | Φ1400 | Φ1500 | Φ1700 | Φ1900 |
Output T/H | 10-15 | 12-17 | 16-22 | 20-28 | 26-35 |
Feeding size mm | 0-40 | 0-40 | 0-45 | 0-50 | 0-55 |
Feeding moisture % | <15 | <15 | <15 | <15 | <15 |
Product fineness % | 8-12 | 8-12 | 8-12 | 8-12 | 8-12 |
Product moisture % | <1 | <1 | <1 | <1 | <1 |
Power of main motor Kw | 200 | 200 | 280 | 315 | 400 |
Feeding ar temperature ℃ | <450 | <450 | <450 | <450 | <450 |
Discharge air temperature ℃ | 80-95 | 80-95 | 80-95 | 80-95 | 80-95 |
Air discharging volume M3/H | ~40000 | ~45000 | 65000 | 80000 | 100000 |
Weight T | 45 | 52 | 75 | 96 | 100 |
If you want to know more about vertical roller grinding mill equipment, please leave us a message or chat with our on line service now.