Problems and solutions in the production process of slag ultra-fine vertical mill
After the slag ultra-fine vertical mill is produced for a period of time, some users will encounter various equipment failure problems. Some users will buy second-hand equipment or some informal small factories, many small factories do not have quality assurance and after-sales service. When the user does not have a professional technical staff, it will be difficult to solve the fault and ask for help everywhere, which will cause the equipment to be shut down for a long time and cannot be produced. For this reason, we summarizes the following problems and solutions in the production process of the superfine slag vertical mill.
Superfine slag vertical mills have direct problems for users in the production process. The main problems are excessive equipment noise or vibration, no powder output or reduced output, and the powder becomes coarse or fine.
The main noise or vibration of the slag ultra-fine vertical mill is too loud. The possible causes and solutions are as follows: the grinding roller does not rotate, which requires disassembly and washing of the grinding roller device; the grinding ring is loose and the grinding ring needs to be tightened; falling into the metal Objects, check whether there are any metal objects inside the machine body falling into it, and remove it; uneven feeding and less feeding, need to adjust the feeding amount; the two halves of the coupling have different shafts, and the coaxiality of the coupling needs to be calibrated; The roller is worn out, deformed out of round, and the grinding roller needs to be inspected and replaced in time; the foundation is not strong, and the foundation needs to be reinforced.
The powder is too coarse or too fine during the grinding process. On the one hand, the speed of the classifier does not match the required grading particle size of the material, and the speed of the classifier must be adjusted; on the other hand, the air volume of the blower is not appropriate, if the powder is too coarse , When adjusting the speed of the classifier can not reach it, you can properly close the valve of the air inlet pipe of the blower. If the powder is too fine, you can reduce the speed of the classifier or remove the classifier to increase the speed of the blower.
The slag ultra-fine vertical mill has no or less powder output due to the following reasons: the discharge valve (air lock) is not tightly closed, the outside air and dust are sucked backwards, and the discharge valve needs to be repaired; main engine wind If the channel is blocked, the blockage should be removed; the blade is worn, resulting in too little or unable to shovel material, so check the wear of the blade and replace the blade; the pipe and flange joints are seriously leaking, and the leak should be carefully checked. Reseal the air.
In addition, various other problems will occur after the long-term operation of the slag ultrafine vertical mill, some of which are even difficult problems, which require very experienced professionals to solve. To
No mechanical equipment can guarantee that there will be no failures during operation, and no matter how strong the manufacturer is, it dare not say that their products will not have problems. When choosing enough equipment to buy equipment, in addition to comparing the quality of the product itself, it is also necessary to conduct a comprehensive and in-depth investigation on whether the company's after-sales service is complete to ensure that the equipment can continue to operate smoothly for a long time after installation.
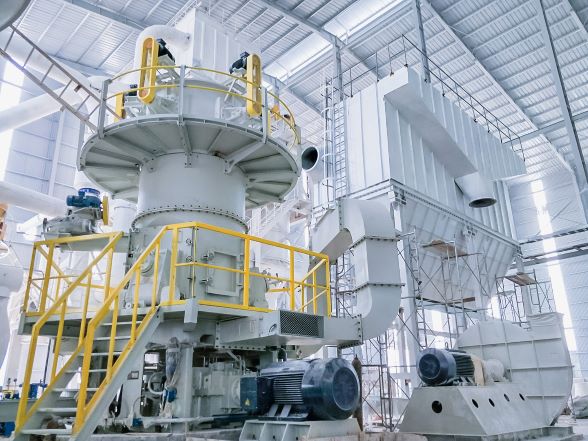
1. Compulsory repair method This method is to formulate a specific plan in advance for the repair date, category and content of the slag ultra-fine vertical mill, and proceed in strict accordance with the plan, regardless of the actual technical status of the vertical mill equipment. The advantage is that it is convenient to make adequate preparations before repairs, and can effectively ensure the normal operation of the vertical mill equipment.
2. The regular repair method is based on the actual use of theslag ultra-fine vertical mill, referring to the relevant maintenance cycle, and formulating the planned date and approximate repair workload of the vertical mill equipment. This method is conducive to preparing for repairs.
3. Repair method after inspection This method prescribes the inspection plan of the slag vertical mill in advance, and determines the repair date and content based on the inspection results and previous repair data. This method is simple and easy to implement, but poor mastery will affect the preparation before repair.
4. Partial repair method is characterized in that the various parts of the slag ultra-fine vertical mill are not repaired at the same time, but are repaired according to the independent parts of the equipment, and repaired separately in order, and only part of it is repaired each time. The advantage of this method is that because the repair workload is scattered and divided into zero, it can be repaired in holidays or non-production time, which can increase the production time of the equipment and increase the utilization rate of the vertical mill equipment.
5. Component repair method: Remove the slag ultra-fine vertical mill components that need to be repaired and replace them with the same components that have been prepared in advance. The components are also replaced by simple "insertion" and "pull out" methods. The advantage of this method is that it can save disassembly. The disadvantage of installation time is that a certain amount of spare parts is required, which takes up a lot of money.
6. Synchronous repair method refers to several slag ultra-fine vertical mills that are closely related to each other in the production process, and they are arranged to be repaired at the same time to realize the synchronization of repairs, so as to reduce the downtime of decentralized repairs.
Superfine slag vertical mills have direct problems for users in the production process. The main problems are excessive equipment noise or vibration, no powder output or reduced output, and the powder becomes coarse or fine.
The main noise or vibration of the slag ultra-fine vertical mill is too loud. The possible causes and solutions are as follows: the grinding roller does not rotate, which requires disassembly and washing of the grinding roller device; the grinding ring is loose and the grinding ring needs to be tightened; falling into the metal Objects, check whether there are any metal objects inside the machine body falling into it, and remove it; uneven feeding and less feeding, need to adjust the feeding amount; the two halves of the coupling have different shafts, and the coaxiality of the coupling needs to be calibrated; The roller is worn out, deformed out of round, and the grinding roller needs to be inspected and replaced in time; the foundation is not strong, and the foundation needs to be reinforced.
The powder is too coarse or too fine during the grinding process. On the one hand, the speed of the classifier does not match the required grading particle size of the material, and the speed of the classifier must be adjusted; on the other hand, the air volume of the blower is not appropriate, if the powder is too coarse , When adjusting the speed of the classifier can not reach it, you can properly close the valve of the air inlet pipe of the blower. If the powder is too fine, you can reduce the speed of the classifier or remove the classifier to increase the speed of the blower.
The slag ultra-fine vertical mill has no or less powder output due to the following reasons: the discharge valve (air lock) is not tightly closed, the outside air and dust are sucked backwards, and the discharge valve needs to be repaired; main engine wind If the channel is blocked, the blockage should be removed; the blade is worn, resulting in too little or unable to shovel material, so check the wear of the blade and replace the blade; the pipe and flange joints are seriously leaking, and the leak should be carefully checked. Reseal the air.
In addition, various other problems will occur after the long-term operation of the slag ultrafine vertical mill, some of which are even difficult problems, which require very experienced professionals to solve. To
No mechanical equipment can guarantee that there will be no failures during operation, and no matter how strong the manufacturer is, it dare not say that their products will not have problems. When choosing enough equipment to buy equipment, in addition to comparing the quality of the product itself, it is also necessary to conduct a comprehensive and in-depth investigation on whether the company's after-sales service is complete to ensure that the equipment can continue to operate smoothly for a long time after installation.
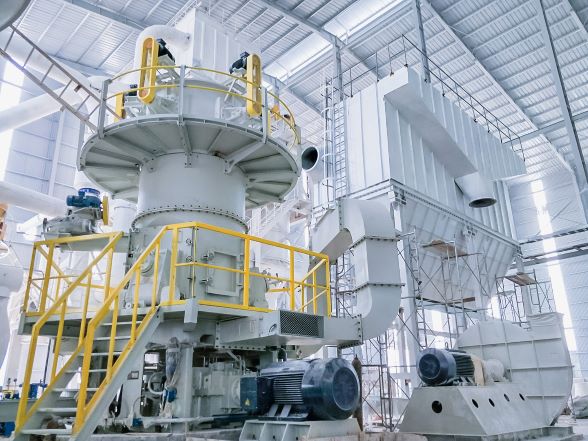
What are the methods for daily maintenance of slag vertical mill equipment
After the slag ultra-fine vertical mill has been put into operation for a period of time, a series of overhauls and maintenance measures must be carried out, such as overhauling the internal parts of the slag vertical mill, replacing the lubricating oil, and removing dust, etc., to protect the slag vertical mill and reduce Its parts are worn out and its service life is prolonged. Now the maintenance methods and maintenance methods of slag vertical mill equipment are sorted out as follows, hoping to help customers.1. Compulsory repair method This method is to formulate a specific plan in advance for the repair date, category and content of the slag ultra-fine vertical mill, and proceed in strict accordance with the plan, regardless of the actual technical status of the vertical mill equipment. The advantage is that it is convenient to make adequate preparations before repairs, and can effectively ensure the normal operation of the vertical mill equipment.
2. The regular repair method is based on the actual use of theslag ultra-fine vertical mill, referring to the relevant maintenance cycle, and formulating the planned date and approximate repair workload of the vertical mill equipment. This method is conducive to preparing for repairs.
3. Repair method after inspection This method prescribes the inspection plan of the slag vertical mill in advance, and determines the repair date and content based on the inspection results and previous repair data. This method is simple and easy to implement, but poor mastery will affect the preparation before repair.
4. Partial repair method is characterized in that the various parts of the slag ultra-fine vertical mill are not repaired at the same time, but are repaired according to the independent parts of the equipment, and repaired separately in order, and only part of it is repaired each time. The advantage of this method is that because the repair workload is scattered and divided into zero, it can be repaired in holidays or non-production time, which can increase the production time of the equipment and increase the utilization rate of the vertical mill equipment.
5. Component repair method: Remove the slag ultra-fine vertical mill components that need to be repaired and replace them with the same components that have been prepared in advance. The components are also replaced by simple "insertion" and "pull out" methods. The advantage of this method is that it can save disassembly. The disadvantage of installation time is that a certain amount of spare parts is required, which takes up a lot of money.
6. Synchronous repair method refers to several slag ultra-fine vertical mills that are closely related to each other in the production process, and they are arranged to be repaired at the same time to realize the synchronization of repairs, so as to reduce the downtime of decentralized repairs.